

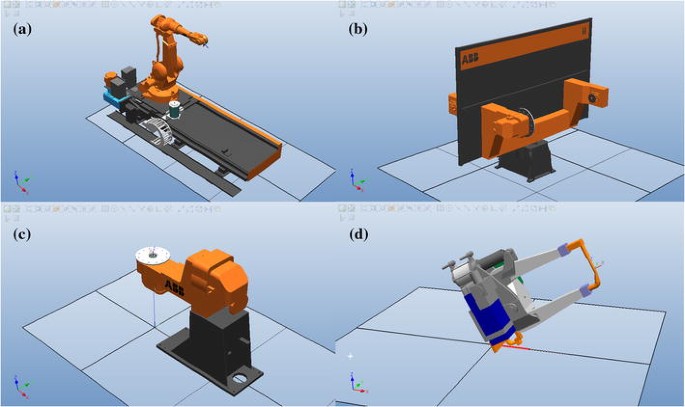
In the centre of the workspace, directly above and below the base joint there is a column, inside which there are also some restrictions on robot movement. The workspace of a UR arm is spherical, and in the working area diagrams that you’ll find under the support site it’s represented with two concentric circles, a smaller one labelled “Recommended Reach” and a slightly larger one labelled “Max. Here we will broadly categorise these situations as singularities, and explain them one by one. There are three main scenarios where a UR robot may have problems moving to a position, either because it is physically not possible for the robot to reach the required position, or because it’s not possible to get there from the current position of the robot joints.

We call this conversion process kinematics, and with articulated robot arms like those in the UR product range, there are inevitably some difficulties with this conversion in certain situations. The robot itself however needs this to be converted into a target angle for each of its six joints in order to be able to move the tool to the intended position. When programming a robot to do a task, we generally think in terms of the way the robot tool moves in its workspace and describe this as movements relative to X, Y and Z axes in 3D or Cartesian space. gif files, they will load after some seconds, wait for it to fully load it to understand the concepts.
